Quartz sand, also known as silica sand, is a common non-metallic mineral raw material, which can be made into high-purity quartz sand after beneficiation and purification. Widely used in industries such as glass, ceramics, metallurgy and refractory materials, and other fields involving optical fiber, military, and aerospace industries. These fields have extremely strict requirements on the purity of quartz sand raw materials, requiring very low impurity content in quartz sand. In quartz sand, the main mineral is quartz. In addition to impurities containing iron elements, it often contains some other impurity minerals. Among them, mica often exists in the parent rock of sandstone raw materials such as marble and granite. However, sand and gravel aggregates have strict regulations on the content of mica, and the content of free mica in the finished sand is required to be ≤ 2%. Quartz sand processing mainly through crushing and screening, gravity concentration, magnetic separation, flotation, winnowing methods to achieve the effect of removing mica impurities.
What is Mica
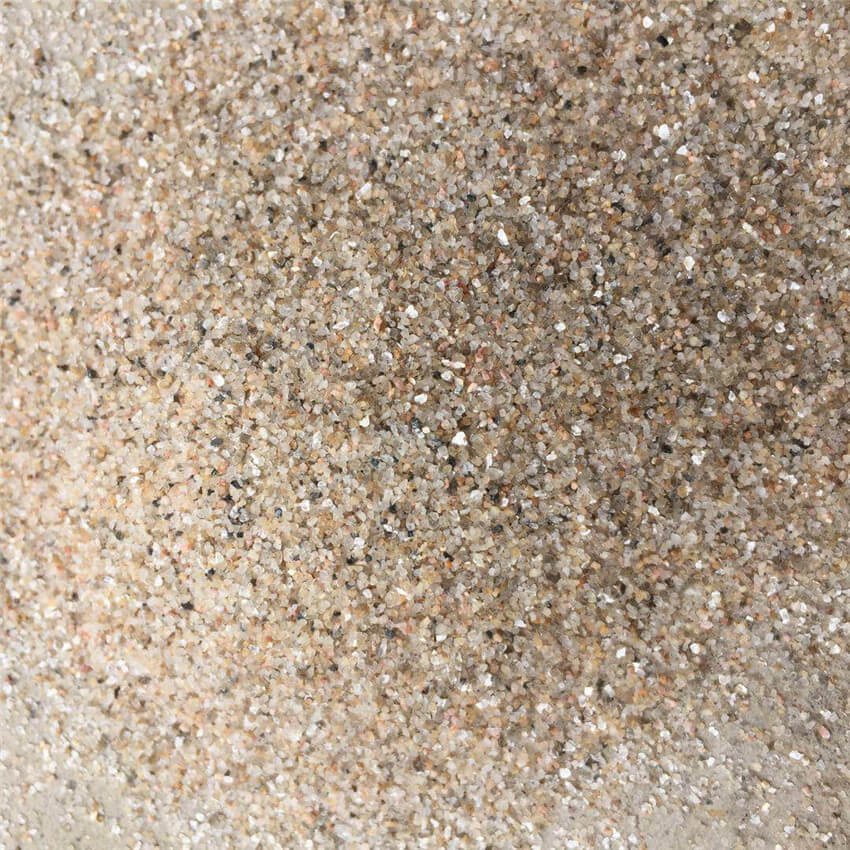
Mica is one of the often associated minerals of quartz sand. For quartz sand, mica is an impurity. The removal of mica is an important part of quartz sand purification. It is a general term for mica group minerals, and it is aluminosilicate of potassium, aluminum, magnesium, iron, lithium and other metals, all of which are layered structure and monoclinic crystal system. The crystals are pseudo-hexagonal flakes or plates, occasionally columnar. The lamellar cleavage is very complete, with glass luster, and the flakes are elastic. There are biotite, phlogopite, muscovite and so on.
Methods of removing mica from quartz sand
1. Crushing, screening and separation
During the crushing process, there is obvious selective crushing of mica and other paragenetic minerals, and the mica minerals are still in flake shape after crushing. Other minerals are in irregular granular shape, and are sieved with the help of the difference in the shape of the crushed products to realize the separation of mica from quartz.
(1) The sand and gravel processing system that needs to remove mica can consider choosing the corresponding crusher. The impact crusher can be used in the medium crushing and fine crushing stages, because the crushing method is impact crushing, and the ore can be selectively crushed along the cleavage plane and bedding plane. Especially for the mica embedded in the ore and the thick sheet mica, the impact crusher can effectively separate it from the gangue.
(2) Ball mill are widely used in the sand making process of hydropower engineering sand and gravel processing systems. When the rod mill grinds ore, the rods are in line contact, which has the characteristics of crushing bulk materials and protecting fine-grained and layered materials. The fine-grained mica in the ore can be dissociated from the rod-milled materials.
(3) There are a large number of vibrating screens in the sand and gravel processing system. The appropriate screen hole size and screen hole form can be selected according to the mica embedding particle size in the raw ore, and multiple screening forms can be used together. Due to the difference in the properties of raw ore, targeted crushing, screening and sorting tests can be carried out before designing the sand and gravel processing system. Select the appropriate type of crusher and vibrating screen to achieve better mica separation effect.
The process of this method is simple, less equipped equipment, high production efficiency, and strong sorting ability. The required sorting equipment is basically the same as the main processing equipment of the sand and gravel processing system, and can be applied to the sand and gravel processing system. Quartz beneficiation can be realized by carrying out targeted mica-removing transformation on the ordinary crushing and screening process.
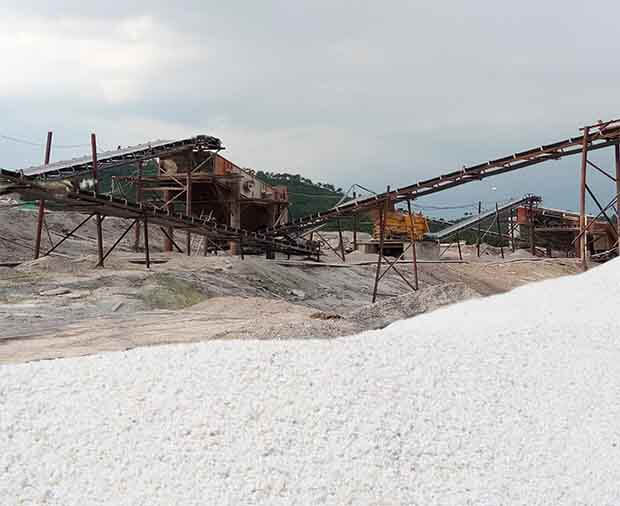
2. gravity separation
According to the nature of the ore, there is little difference in the density of mica and its symbiotic minerals. However, mica is in the form of obvious flakes, while other minerals are basically granular. Grind the raw ore to a certain size and place it on a shaking table. Because of the thinner sheet size, the mica can be enriched and stratified in the light mineral zone. While other minerals are enriched in the heavy mineral belt, so as to realize the sorting of mica.
The shaking table gravity separation method has simple process and good separation ability. However, additional equipment such as a shaking table is required, and the energy consumption is high, the water consumption is large, and the site is occupied. Before considering it, the sand and gravel processing system needs to carry out the shaking table sorting test on the crushed ore, and weigh the pros and cons according to the sorting effect.
3. Magnetic separation
Mica minerals such as biotite and iron lithium mica contain iron, which are weak magnetic minerals. Such mica minerals can be sorted by magnetic separation. Tests have shown that the mica content in the finished sand is greatly reduced after magnetic separation to remove mica. It can be controlled within 2%, which meets the sand standard, and the concrete mixing performance produced by de-mica machine-made sand is better.
Some mica has weak magnetism and can be removed by magnetic separation, which can remove iron-containing mica. Before considering the magnetic separation operation, the gravel processing system needs to conduct chemical analysis on the properties of the raw sand and gravel and the mica minerals contained in it. Determine whether it contains iron, and conduct a magnetic separation test according to the iron content.
4. Wind selection
The air separation method is a gravity separation method with air as the separation medium. It has a wide range of applications and can separate ores with different densities, particle sizes, shapes, types, and properties in the moving air flow. After the raw ore is crushed, the shape of the ore changes. Mica has a certain degree of elasticity. When crushed together with other minerals, mica is easy to squeeze and peel off, while other brittle minerals are crushed into fine particles. When the minerals in the same particle size fall naturally by gravity, the wind resistance of the flaky mica is greater than that of the granular gangue minerals, and the falling speed is slower, so as to realize the separation from the gangue minerals.
At present, there are many types and models of air separators, and the technology is mature, which can be directly used in sand and gravel processing systems. The principle of air separation is similar to that of the sand and gravel system dust collector, which requires the raw ore to be kept dry, so the air separation method is only suitable for dry production of sand and gravel processing systems.
5. Flotation separation
Separating is carried out according to the difference in the physical and chemical properties of the surface of mica and quartz sand. The quartz ore is crushed and grinded to dissociate the mica monomer. Under the action of the medicine, the mica becomes a foam product and is separated from the gangue. Mica flotation can be carried out in acidic or alkaline pulp, and the cations of long carbon chain amine acetates and anions of fatty acids are mica collectors.
The flotation method is mainly used in the recovery of crushed mica and fine-grained mica in the sand and gravel industry, especially the mica resources in the tailings. In actual production and application, the preliminary process flow should be determined according to the nature and characteristics of the actual ore. Then enrich and optimize the process through a series of condition tests to obtain better technical and economic indicators.
The method of removing mica from quartz sand mainly includes a combination of crushing, grinding, washing, re-selection, magnetic separation and other beneficiation processes. The specific selection can be determined according to the composition information of the ore and the needs of the customer. The purpose is to remove impurities in quartz sand and make a purer and higher-grade concentrate.
High-purity quartz has become an irreplaceable key raw material in high-tech fields such as new energy, optical fiber, laser, information technology, aerospace, and microelectronics. Due to the different properties of quartz ore in different regions, the impurities contained and particle size of embedded parts are also different. Therefore, when the pretreated quartz sand is further purified and prepared, it is necessary to adopt different joint processes according to the ore properties of the quartz sand itself, so as to remove impurities in a targeted manner and obtain high-purity quartz sand. JXSC have more than 38 years of experience in quartz sand/silica sand beneficiation process, professional engineers will configure mineral processing solutions and equipment for you, 100% factory price!