Barite is an important barium-containing mineral. It is widely used in petroleum, chemical, paint, filler and other industrial sectors because of its high density, low hardness, stable chemical properties, non-toxicity, and absorption of radioactive rays. Among them, 80~90% are used as mud weighting agent and paint in oil drilling, and it is an important strategic non-metallic mineral. At present, the proportion of barite commercial grade bonanza grades higher than 90% has declined, and the grade of BaSO4 in most deposits is 50% to 90%. However, with the expansion of its application fields and the accelerated consumption of resources, the high-grade barite ore that is easy to select has been gradually reduced, and it often coexists with various types of minerals, which can only be used after beneficiation process.
About Barite
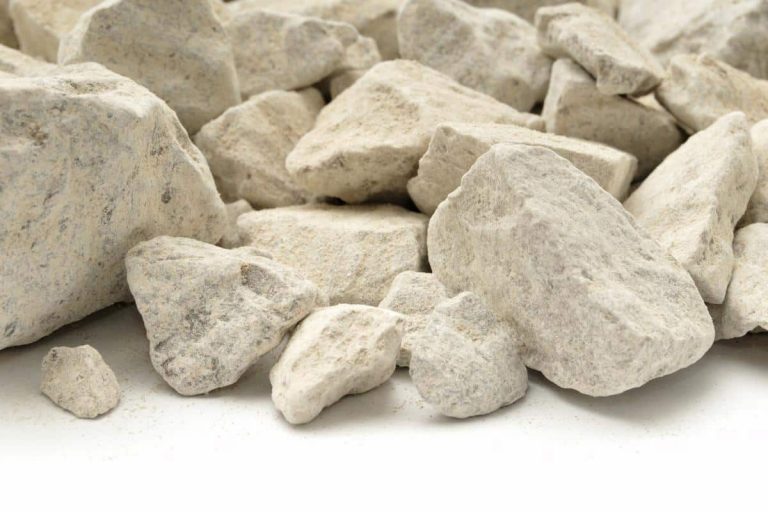
Barite is a non-metallic mineral product with barium sulfate as the main component. It is the most widely distributed barium-containing mineral in nature and is produced in low-temperature hydrothermal veins. Often associated with minerals such as quartz, calcite, dolomite, fluorite, siderite, rhodochrosite, pyrite, galena and sphalerite. In addition, in some metal deposits, such as lead, zinc, gold, silver and rare earth deposits, barite is often a common gangue mineral. Because of its large proportion in non-metallic minerals and obvious crystalline aggregates, it is called “barite”.
Barite Beneficiation process methods
Barite is brittle and brittle, and the crystals are large tubular. For the separation of barite, the general beneficiation methods include gravity separation, magnetic separation and flotation.
1. Gravity separation
The process has the advantages of simple equipment, good stability, no beneficiation agent, low cost, and less environmental pollution.The barite gravity separation method is mainly based on the density difference between barite and associated minerals. Including ore washing, screening, desliming, jig separator, shaking table and other technological processes, it is mostly used for the treatment of residual barite ore. A single gravity separation process is difficult to efficiently recover barite resources, and it is necessary to combine magnetic separation or flotation processes to further recover barite.
2. Magnetic separation
For barite ore containing magnetic iron minerals with fine particle size, strong magnetic separation is often used to separate iron-containing minerals and barite. This process has the advantages of high production efficiency, low energy consumption and less environmental pollution. The disadvantage is that it is difficult to handle fine-grained ore and cannot separate non-magnetic gangue. Therefore, for barite ore containing non-magnetic gangue, it is difficult to obtain high-quality concentrate with a single magnetic separation. Generally, a combined gravity separation or flotation process is required to further separate the barite. It is often used to select some iron-bearing minerals such as siderite barite ore.
3. Flotation separation
The barite flotation method is mainly based on the difference in surface physical and chemical properties between barite and associated minerals. It is commonly used in sedimentary barite ores and hydrothermal barite ores associated with sulfide ores and fluorite.The interaction between collectors and barite minerals has a large impact on the grade and recovery of barite concentrates. At the same time, when flotation separates the associated minerals with similar floatability to barite, an effective inhibitor can increase the floatability difference between the two, which is also one of the keys to barite flotation separation. Therefore, in the flotation process of barite ore, both inhibitors and collectors play a very important role. Under conventional flotation conditions, the barite recovery rate can reach more than 80%. The flotation method must be used for the separating of ores with finely embedded particle size and gravity tailings.
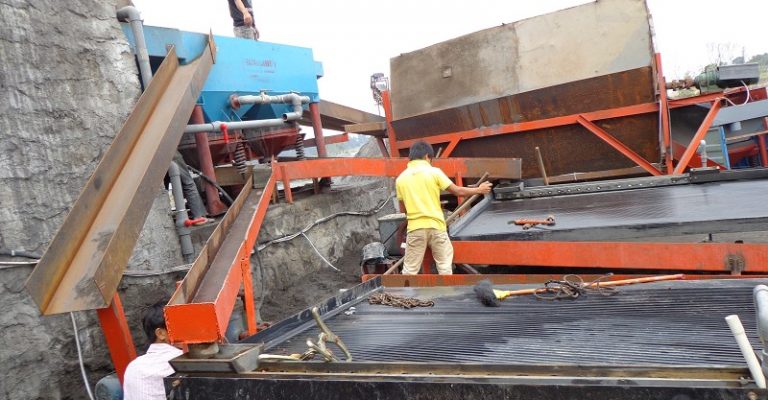
Configure beneficiation process Plant
According to the specific physical and chemical properties of barite, with reasonable equipment and scientific technology, the combined beneficiation production can meet the needs of normal production. The configuration of barite beneficiation production line needs to be determined according to the following ore factors. .
1. Inlaid grain size of barite
The inlaid particle size of barite directly affects the particle size of its crushing, so it involves the configuration of the crusher and the vibrating screen. The general barite ore is coarse-grained inlaid, and the barite crystals are coarser and heavy. The spar ore itself is brittle and fragile, which requires the use of a simple and practical jaw crusher for coarse crushing to avoid the production of excessive powdery ore. For barite ore with finely embedded particle size, it is necessary to configure jaw crusher, roller crusher and other crushers according to the situation, so as to achieve the beneficiation effect. For the screening of fine-grained inlaid barite ore, linear vibrating screens are mostly used.
2. Mud content of barite ore
The mud content of barite ore directly affects its beneficiation effect. In order to avoid the negative impact of the mud content on the beneficiation index, it is necessary to de-slime in advance, which requires the use of a trommel washer. Commonly used barite washing machines include spiral washing machines and trough washing machines. For barite ore with no mud or less mud content, it is not necessary to consider the washing equipment and washing process.
3. The separated particle size of barite
The selected particle size of barite refers to the particle size of barite selected by the jig machine. Most of the barite can be dissociated as monomers below 30mm, which can be directly sorted by a large particle jig. For fine-grained barite ore, it needs to be crushed to below 6mm and sorted by trapezoidal jig.
4. Processing capacity of barite concentrator
The processing capacity of the barite concentrator will affect the configuration of the number and size of the barite jig. Understanding the processing capacity of the barite ore plays an important role in the configuration of the jig.
5. Dewatering of barite
Since barite beneficiation adopts jig as sorting equipment, its concentrate and tailings are discharged out of the machine with a large amount of water. In order to return the excess water source to the circulation system for continuous use, and for the concentrate and tailings to be directly transported to the destination site for storage or bagging. Under normal circumstances, it is necessary to dewater the barite concentrate and tailings, which will use dewatering screen equipment. Of course, dehydration equipment may not be used for plants with natural dehydration conditions.
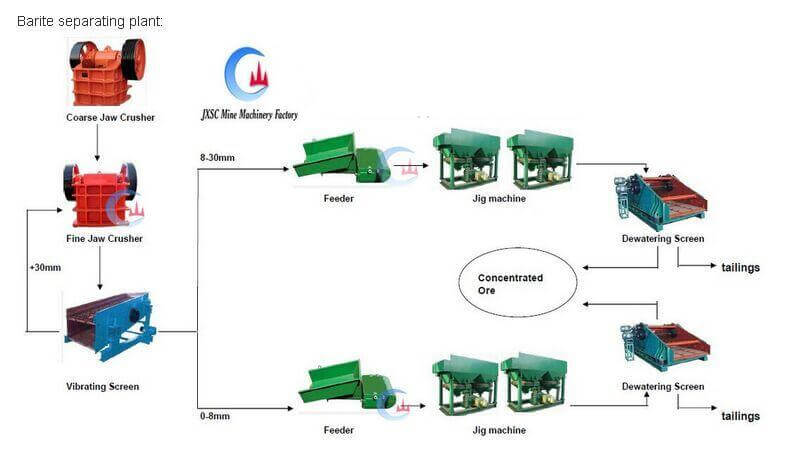
With the low grade of barite ore and the complexity of ore properties, gravity separation, magnetic separation, flotation and combined beneficiation methods are gradually widely used in barite ore separation. Under normal circumstances, barite beneficiation is mainly carried out by the method of gravity separation, including jaw crusher, vibrating screen, jig, dewatering screen and other equipment. JXSC are a professional manufacturer of beneficiation solutions, providing scientific and reasonable barite beneficiation plant, mining equipment and process design, low cost, high recovery rate, and online consultation with professional engineers.