Tungsten is an important strategic metal, widely used in modern technology in pure metal state and alloy state. The pure metal of tungsten is silver-white and has high hardness, strength and wear resistance. Alloy steel, tungsten carbide-based cemented carbide, wear-resistant alloy and strong heat alloy are the main alloying states of tungsten. Tungsten is widely used in electrical, metal rolling, machining, geotechnical engineering, aerospace, military, etc. At present, the main uses of tungsten are in the manufacture of cemented carbide, filament, high-speed cutting alloy steel and heat-resistant special steel, rocket propeller nozzles and firearms. Therefore, the tungsten ore beneficiation process is becoming more and more important.
Tungsten ore
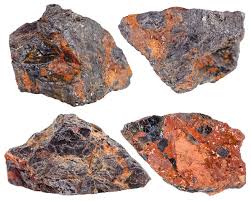
Tungsten ore is a rare metal that is widely distributed and exists in almost all kinds of rocks. Due to its low content, it can only be enriched through relevant geological processes before forming ore deposits for mining. At present, more than 20 types of tungsten ore have been found in nature, among which scheelite and wolframite are more valuable for mining and are also the main source types of tungsten ore resources.
Tungsten ore Beneficiation Process
How is tungsten extracted from its ore?
The main beneficiation methods for tungsten ores are physical methods such as pre-concentration, gravity concentration, flotation and magnetic separation; as for the refractory middling ore and low-grade concentrate, prefer to chemical concentration way.
1. Beneficiation processing of Tungsten ore
Wolframite property: tungsten from wolframite ore mostly in quartz vein type, high dilution rate, low grade, coarse particle size, high density, low hardness, easy sliming and deep color. Wolframite mineral processing method mainly in gravity separation, and includes four parts: pre-selection, gravity separation, concentration and recovery.
- Pre-selection ore washing, desliming and classification should be carried out before the pre-selection, the pre-selection methods have hand picking, photoelectricity picking, and heavy medium separation, etc.
By pre-selection and discarding the waste rock which accounts for 50% of the raw ore, the WO3 grade of the ore is enriched from 0.25% ~ 0.3% to 0.45% ~ 0.8 %, and the recovery is 96% ~ 98 %. - Gravity separation adopts a combination of jig machine and shaking table to recover coarse tungsten ore.
According to different gravity separation working principle, gravity separator can be subdivided into a shaking table, mineral jig, spiral chute and centrifugal separator.
(1). Shaking table is one of the most widely used gravity equipment for separating fine materials. Compared with the cone concentrator, spiral concentrator and other fine particle separation equipment, the processing capacity of the shaking table is lower. But it has such outstanding advantages as a high enrichment ratio, the final concentrate can be obtained after one separation and wide application range.
(2). Jigging machine is the main beneficiation method for wolframite, it has the great characteristics of large particle size, high treatment capacity, high separation efficiency and low water consumption. It is excellent equipment for gravity separation of coarse and medium-sized ores and has been widely used in wolframite mines.
(3). The Centrifugal concentrator force produced by the high-speed rotation of the concentrator strengthens the gravity separation process and makes the recovery of the fine particles more effective. - Magnetic separation: Wolframite has weak magnetic properties, the high-intensity magnetic separation equipment ( such as SLon vertical high gradient strong magnetic separator ) do a great help for wolframite recovery.
- Flotation separation:The flotation process is usually used to treat extra fine wolframite slime.
Fine flotation requires high selectivity of collectors, such as arsonic acid, phosphonic acid, chelate, amphoteric collectors and a few fatty acid collectors. Among them, arsonic acid and phosphonic acid collectors have certain toxicity, are easy to bring about environmental pollution problems, and have high manufacturing costs. Therefore, these kinds of collectors are hardly used in the current flotation process In recent years, the use of hydroxamic acid collectors is a good solution to this problem.
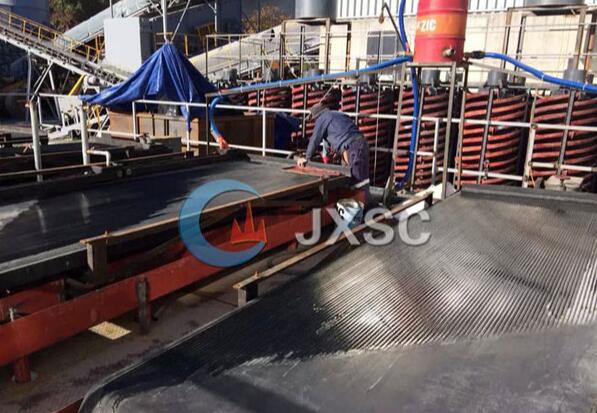
2. Scheelite mineral processing
According to the paragenetic relationship between scheelite and different types of gangue ores, scheelite ores can be divided into different types, and the beneficiation methods for different types of scheelite ores are also different. For example, scheelite-quartz (or silicate) type can be used in combination with gravity separation and flotation separation according to the particle size distribution, while scheelite-calcite-fluorite-barite type can be recovered by flotation separation.
- The separation methods of scheelite are different with different disseminated grain size. For coarse-grained scheelite, generally uses a gravity separation method, which has the advantages of lower cost, less environmental pollution and higher recovery ratio. For fine size scheelite, the separation uses the flotation separation method.
- Scheelite is often associated with a variety of sulfide ore, common molybdenite, chalcopyrite and pyrite, etc. during the beneficiation process, the sulfide ore should be floated out first.
- Scheelite flotation machine is carried out in alkaline medium, adjust slurry PH value in 9 ~ 10 by the sodium carbonate, sodium hydroxide. Common inhibitors are sodium silicate, tannin, various phosphates. Collectors have sodium oleate, tar oil and oxidized paraffin, etc.
- Scheelite has good floatability, but it is often associated with fluorite, calcite, apatite, barite and gangue minerals containing calcium and barium, those have similar floatability, increase the separation difficulty. In order to improve the flotation selectivity of scheelite and calcareous gangue minerals, multi-metal salts, such as iron sulfate, are often used in combination with sodium silicate to improve the flotation effect of scheelite.
3. Mixed wolframite and scheelite beneficiation processing
For the single scheelite and wolframite with simple composition, the separation process is relatively simple. For the paragenetic ore of wolframite and scheelite, especially the paragenetic polymetallic ore of fine-grained wolframite and scheelite, tungsten is usually recovered by a mixed flotation process. There is two main tungsten ore dressing plant design:
(1) Mixed flotation of sulfide ore – mixed flotation of wolframite-heated scheelite concentrate – strong magnetic separation of Scheelite tailings – gravity separation of Wolframite;
(2) Mixed flotation of sulfide ores – strong magnetic separation of wolframite – scheelite flotation-wolframite flotation.
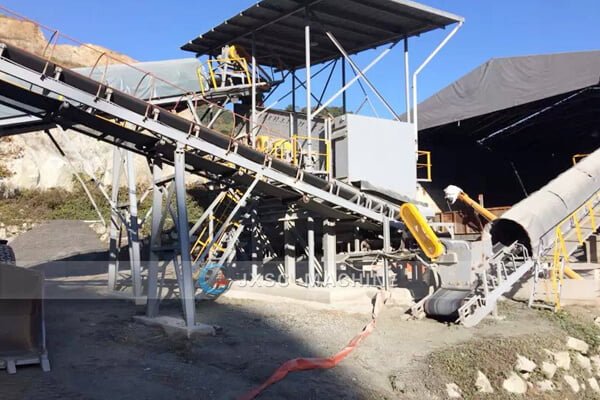
For the separation of tungsten ore, it is necessary to determine the ore composition and refractory degree of tungsten minerals first. It is recommended to find a manufacturer with mineral processing qualifications to conduct mineral processing tests, and customize the process flow according to the actual situation according to the report, in order to effectively separate useful minerals. JXSC supports custom tungsten mineral processing plant, solutions, process design, and high-quality mining equipment.