Crushing equipment is an indispensable part of crushing, sand making, grinding and other processes. However, there are many kinds of crushers in the current market. How to select suitable and satisfactory products? First of all, we need to be familiar with the applicable conditions, advantages and disadvantages of these mainstream devices.
Before understanding the crusher, it is necessary for us to have a simple understanding of the crushing mode.
Crushing Mode
The crushing mode of crusher is divided into extrusion, splitting, breaking, shearing, impact or striking, etc. Generally, there is no single mode of action.
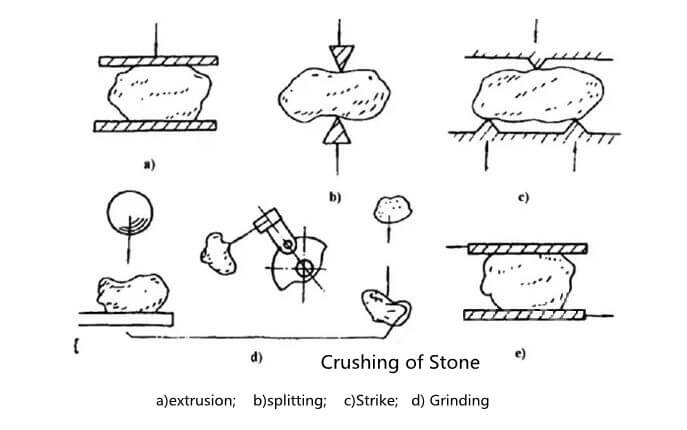
Crushing by Extrusion: The working face of crushing machine exerts pressure on the material sandwiched between them. When the compressive stress of the material reaches its compressive strength limit, it will be crushed.
Splitting Shear Breaking: The edge of the crushing face wedges into the material and causes the internal tensile stress. When the value exceeds the tensile strength limit of the material, the material splits and produces powder locally at the contact point between the sharp edge and the material.
Bending Breaking: Materials sandwiched between working faces, such as simply supported beams or multi supported beams, are mainly subject to bending stress, but are subject to splitting action at the contact of working faces.
Extrusion Shear Fracture: The combination of extrusion fracture and shear fracture.
Impact Crushing: Impact crushing includes the impact of high-speed moving crushing body on the broken material, the impact of high-speed moving material on the fixed wall and the mutual impact of moving materials.
Analysis of crushing mechanism, advantages and disadvantages of different crushers
Crushers can be divided into three categories according to the size of feed and product:
- Coarse crusher: from 1500 ~ 500mm to 350 ~ 100mm;
- Middle crusher:from 350 ~ 100 mm to 100 ~ 40 mm;
- Fine crusher:from 100 ~ 40mm to 30 ~ 10mm.
According to the working principle and structural characteristics, crushers can be divided into:
Advantages: simple structure, reliable work, light weight, low price, small size, low configuration height, large size of feed port, easy adjustment of opening of discharge port, simple maintenance and economic operation cost.
Disadvantages: lining plate is easy to wear, and the content of needle and sheet is high in the product. Generally, the feeding equipment is required.
The cone crusher works continuously. The eccentric motion of the moving cone is used to crush the stone. At the same time, because of the tangential motion between the moving cone and the fixed cone, the stone material must also be subjected to the shearing grinding. Therefore, the working mechanism is the combination of extrusion, shearing and grinding.
Application: mainly used for medium or fine crushing of various stones. According to the different structure (suspension shaft type and supporting shaft type), it can also be used for coarse crushing of stone (less used for suspension shaft type).
Advantages: large crushing ratio, high efficiency, low energy consumption, less dust, uniform product size, stable operation, low failure rate, and not easy to over crush.
Disadvantages: the structure and maintenance are complex, the body is high and the price is expensive.
3. Rotary Crusher
The cycle crusher is continuous crushing, and the principle of laminated crushing is adopted. The crushing process is carried out continuously along the annular crushing chamber.
Application: it is mainly used for coarse crushing of all kinds of hardness materials in the first section, but it is not suitable to break the cohesive ore.
Advantages: large crushing ratio, high capacity, can be full of ore feeding, direct feeding without feeder.
Disadvantages: complex structure, high height and large volume of machine, high need of factory building, large investment in infrastructure construction, heavy machinery, inconvenient handling and high price.
The roller crusher works continuously. The stones are located between two parallel cylindrical moving rollers. The stones are bitten into the roller by the friction between the stones and the rollers. The stones of the smooth roller are squeezed, and the stones of the tooth roller are split and crushed.
Application: mainly used for medium and fine crushing of medium hardness stone (compressive strength below 100MPa) such as coal and limestone. Roller crusher is not used in the processing of pavement crushed stone.
Advantages: simple, compact structure, low investment, convenient adjustment, can be used for crushing viscous materials.
Disadvantages: low production efficiency, hard materials can not be broken.
The impact crusher is a kind of machine which uses the impact energy to break the material. Adjusting the gap between the counter attack frame and the rotor can change the material discharging size and shape.
Application: mainly used for medium and fine crushing of stones with medium hardness, and the shape of crushed stone is better.
Advantages: small volume, simple structure, uniform product size, and selective crushed stone effect, high yield.
Disadvantages: the hammer and counter attack plate are easy to wear, especially the broken hard rock, which is more serious, and needs to be replaced frequently; It is not suitable to break plastic and viscous materials.
Hammer crusher is also continuous in operation, and the stone is broken by using the hammer head on the high-speed rotating rotor.
Application: it is suitable for medium and low hardness and non abrasive stone (compressive strength less than 100MPa) medium crushing and fine crushing. It can also be used for sand making when there are grate bars, but it has been less used.
Advantages: large crushing ratio, high yield and more fine materials.
Disadvantages: the hammer head is worn fast, it needs to be replaced frequently, and the working dust is large, and the viscous materials with water content of more than 12% of raw materials can not pass effectively.
7. Impact Sand Machine(VSI Sand Maker)
The work of impact sand making machine is continuous. It uses high-speed moving materials to punch iron, strike each other and friction between materials to break. There are two kinds of crushing methods: Stone beating and iron beating.
Application: Stone beating is suitable for materials with high abrasion resistance above medium and hard. The finished product has
better grain type and slightly more powder content“ Stone iron beating is suitable for materials with small abrasion under medium and hard, with high crushing efficiency, high cost of wear of the perimeter guard plate and slightly poor grain type of finished products.
Advantages: small energy consumption, high output, large crushing ratio, small equipment volume, easy operation, easy installation and maintenance, plastic function, cubic product, large stacking density, and little wear on the counter attack plate of the machine during operation.
Disadvantages: the maintenance is complex and the cost is high, the general maximum feeding size is not more than 60mm, which is suitable for fine crushing and sand making.
The above crushers are the most commonly configured crushing equipments in gravel sand production line. If you want to know more products, please contact us.