Copper Processing Plant
Advanced Mineral Processing Turnkey Solutions | Eco-friendly Process | ISO Certified Equipment
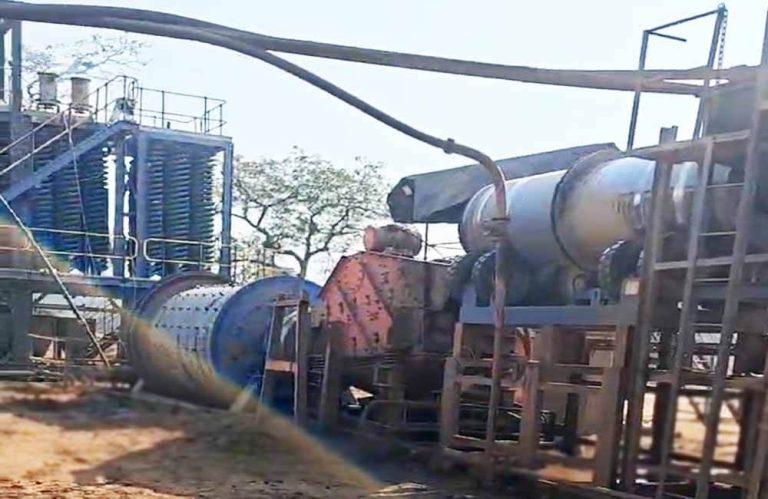
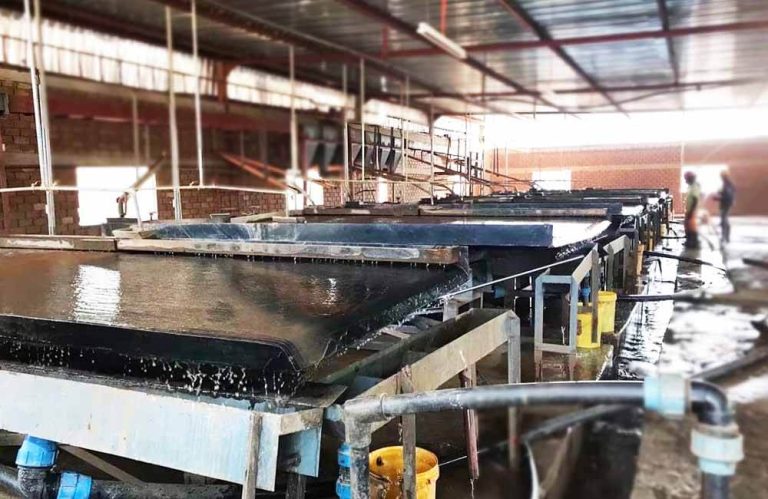
A copper processing plant is an industrial facility designed to extract copper metal from mined ore through beneficiation methods. Copper ore beneficiation usually adopts gravity separation, flotation, magnetic separation, leaching, etc.
JXSC supports customized copper processing plant and equipment, fully suitable for separating copper oxide ore (azurite, cuprite and malachite); copper sulfide ore (chalcopyrite, bornite and chalcocite) and natural copper. It mainly industrial systems that convert copper-containing raw ores into commercial-grade copper concentrates, with a recovery rate of up to 95%+.
copper beneficiation process
Even for the same type of copper ore, it is necessary to design the most appropriate process according to local conditions. Copper ore beneficiation is a process to extract copper from raw ores. Commonly used processes include gravity separation, flotation process, magnetic separation, leaching, and electrolysis.
Copper Extraction Process
Gravity separation: The gravity separation method sorts minerals according to their relative density (usually called specific gravity). Currently, gravity separation is only used to select copper ores with coarser inlays, and is especially suitable for copper oxide ores with higher density.
Flotation separation: Copper flotation process is based on the difference in the physical and chemical properties of the mineral surface, processed by the flotation agent, and the mineral is selectively attached to the bubbles to achieve the purpose of separation. The beneficiation of non-ferrous metal ores, such as copper sulfide ore, lead, zinc, sulfur, molybdenum, etc. is mainly treated by flotation process; some ferrous metals, rare metals, and some non-metallic ores, such as graphite ore, apatite, etc. are also used for the copper flotation process.
Magnetic separation: The magnetic separation method is based on the different magnetic properties of minerals. Different minerals are subjected to different forces in the magnetic field of the magnetic separator, so as to be sorted. It is mainly used for separating ferrous metal ores (iron, manganese, chromium).
- Electrolytic purification process: Cathode copper is a high-purity copper material, commonly used in electronics, electrical, communications, and other fields. After copper ore dressing, if you need to prepare clean cathode copper materials, you need to go through smelting, leaching, electrolysis, refining, etc. Through the copper electrolysis process, remove impurities in crude copper to improve its 99.99% purity to meet the requirements for electrical-grade materials.
Strictly control the process parameters of each link to ensure product quality and cost control, contact us to customize specific copper beneficiation solutions and equipment to meet different needs.
copper Ore Processing Plant
1. Copper flotation process
The setup is complete copper flotation process plant; main equipment and process details as follows:
- Jaw crusher
- Ball mill
- Spiral classifier
- Flotation machine
- Mixing tank
- Thickener
- Disc vacuum filter
Copper Flotation Process Flow
1. Crushing: Adopts two-stage open-circuit crushing and selects jaw crusher for crushing, and the crushed product is transported to fine jaw crusher for two-stage crushing.
2. Grinding: Afterward, the pendulum feeder is transported to the ball mill for grinding and classification, and combined with the classifier, the material reaches below 200 mesh.
3. Flotation separation: After stirring, the pulp enters the flotation machine, and the collector with good selectivity is added for flotation to obtain qualified copper concentrate.
4. Filter & dewatering: The copper concentrate pulp obtained by flotation is transported to a high-efficiency thickener for concentration. Finally, the concentrated bottom flow is filtered and dehydrated by a disc filter to obtain a qualified concentrate.
2. Rock copper processing plant
This setup is a complete rock copper processing plant, including crushing, grinding, gravity separation, drying. Mian equipment and process flow are as follows:
- Jaw crusher
- Impact crusher
- Ball mill
- hydrocyclone
- Spiral chute
- Shaking table
- Slurry pump
- Plate filter press
- Thickener for tailings
- Disc vacuum filter
Rock Copper Ore Processing Flow
1. Crushing and grinding: The chute feeder for feeding raw materials into the primary jaw crusher more stably and smoothly. The primary jaw crusher is used to break large rocks into smaller sizes; the fine jaw crusher is used to break rocks to less than 30mm; the impact tertiary crusher is used to break rocks to less than 10mm. The ball mill cooperates with the cyclone separator to grind 0-10mm materials to 200 mesh.
2. Gravity separation: Pump the 200-mesh slurry into the two-stage spiral chute for primary separation, and then all the heavy ore concentrate will enter the shaking table for re-selection, thereby obtaining high-grade copper concentrate.
3. Tailings treatment: After obtaining the copper concentrate from the shaking table, the concentrate is pumped into the thickener to form a concentrate of suitable density and enters the disc vacuum filter to filter the water to obtain dry copper concentrate. Then, all the tailings enter the conical thickener to be concentrated to a suitable density and enter the plate filter press to recycle the water.
The complete set of equipment can also efficiently separate chromium ore, manganese ore, zinc-lead ore, etc. Contact us to customize the process and machines according to your mineral conditions.
Contact Us Now
Ask us about mineral processing configuration and equipment quote! (No job, No investment)
Notice:
- We only provide mineral processing equipment and solutions; not buy and sell minerals/ ores/ materials.
- We do not recruit, don’t offer jobs, and are not interested in investments or partnerships.
- We value your privacy and keep your information safe.