Manganese Ore processing
40+ Years Experience in Mineral Processing Solutions | ISO Certified Equipment
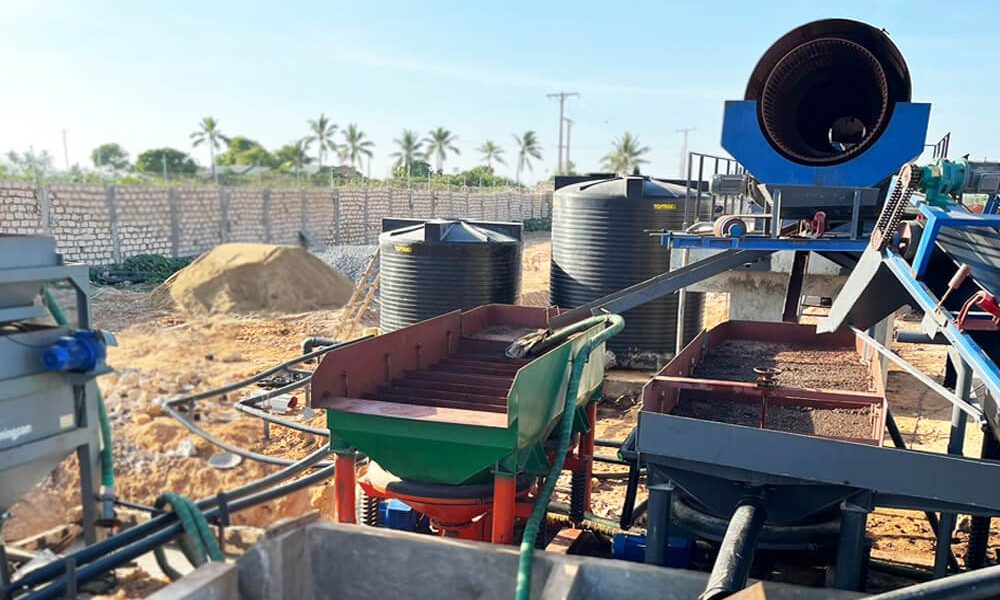
Manganese ore processing mainly includes crushing, washing, gravity separation, magnetic separation, and flotation processes, etc. After beneficiation, the ore becomes more valuable and can be used in various industries such as steelmaking and alloys. Our patented beneficiation system ensures Mn content reaches 95%+ recovery rate and purity.
Application: beneficiation of the manganese oxide ore, carbonate manganese ore, manganese-containing iron ore and multi-metal composite manganese ore.
manganese Beneficiation Process
Manganese ore beneficiation is the process of extracting valuable minerals and removing impurities from manganese ore. It usually includes crushing, grinding, washing, gravity separation, flotation, or magnetic separation processes to improve the grade and recovery of manganese.
beneficiation of manganese ore
1. Pre-separation: usually includes crushing and grinding to reduce the size of the ore particles; sometimes a washing process is also used to effectively remove impurities such as soil and clay adhering to the surface of the manganese ore.
2. Separation stage:
- Gravity separation: A method of using gravity differences to separate and enrich manganese minerals in ores; usually suitable for situations where the density difference between manganese minerals and waste rocks is large. Its equipment includes jig separators, shaking tables, spiral chutes, etc.
- Magnetic separation: It mainly separates the manganese iron oxide. Manganese minerals are attracted to magnetic fields, while impurities are not.
- Flotation process: It separates manganese ore by adding chemicals to make the surface of ore particles hydrophilic or hydrophobic. It mainly beneficiates manganese ores containing non-metallic impurities such as silicates.
Usually, the combined beneficiation process is used for design a manganese ore processing plant according to the characteristics of the ore, to maximize the mineral grade and recovery rate. Contact us to get more manganese ore beneficiation process details and mining equipment quote!
manganese ore Processing plant
Rock Manganese Ore Process plant
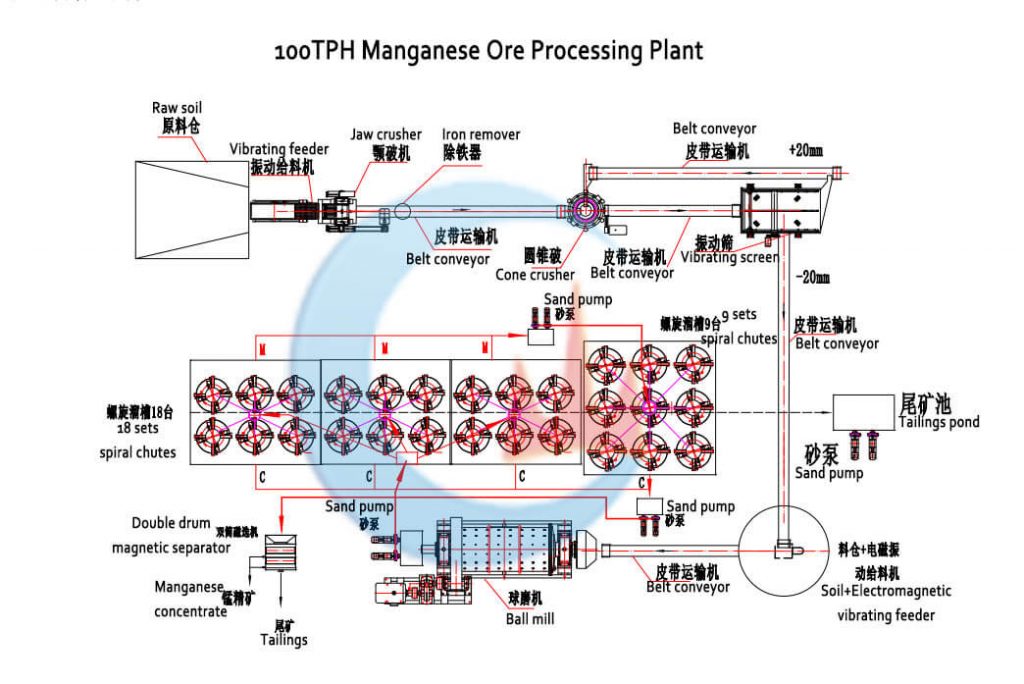
This setup is for the rock manganese ore beneficiation plant, main equipment and flow including:
Rock Manganese ore processing plant flow
- The raw bin + vibration feeder for feeding materials to the jaw crusher automatically, you only need to load the materials into the raw bin by truck or excavator, or other as you want. The jaw crusher is for crushing the raw ore into small pieces, then to the cone crusher to get the fine sizes. The vibration screen for separating the size +20mm back to the cone crusher, 0-20mm will be sent to the ball mill by electromagnetic feeder.
- The ball mill is for grinding the 0-20mm materials to 0-1mm, then using the slurry pump to transport the 0-1mm materials to the spiral chute to separate the heavy minerals.
- The double drum magnetic separator is for separating the manganese from other heavy minerals, making the manganese concentrate to a higher grade.
Advantages of JXSC Rock Manganese Ore Process Plant
- Recycling rate up to 95%+.
- High efficiency and low energy consumption.
- Wear-resistant equipment ensures continuous operation.
From crushing, grinding, to precise gravity separation equipment, efficient separation and enrichment of manganese ore are achieved. Contact us to get more manganese processing plant flow details!
Alluvial & Rock Manganese processing plant
This setup is a 30tph alluvial and rock manganese ore processing plant, the main equipment and process details as follows:
Alluvial & Rock Manganese processing plant flow
(1) The raw ore is fed into the hopper by an excavator, with a vibrating feeder (with a 75mm gap grid) under the hopper. More than 75mm material is directly transported by a belt conveyor to the hopper in front of the crusher.
(2) The materials smaller than 75mm are evenly fed into the trommel scrubber to wash the sticky clay. The rotary scrubberhas 2 layers of screens (mesh 2mm and 20mm). It can screen out three different sizes: 0-2mm, 2-20mm, 20-75mm.
(3) The content of the 0-2mm part is about 33%, which directly enters the 1st and 2nd jig separators for separation. The concentrate from the jig separator will enter the two drum magnetic separators to refine manganese again.
(4). The content of the 2-20mm part is also about 33%, which is fed into the 3rd and 4th jigs for gravity separation with a connecting steel chute. The larger 20-75mm size is transported to the hopper before the crusher and mixed with particles > 75mm. Below the hopper, a trough feeder is used to feed the material into a jaw crusher to be crushed into material less than 40mm; then it is transported to two hammer crushers for fine crushing. The discharge will be pumped to the 5th and 6th jigs by a mud pump.
(5) The concentrate produced by the jig will enter two drum magnetic separators to refine the manganese concentrate again. The tailings produced by the jig and magnetic separator will enter the tailings pond and can be transported away by a mud pump.
Advantages of JXSC Alluvial & Rock Manganese Processing Plant
- Modular design, low cost, fast production.
- Equipment 100% factory direct price.
- High safety, environmental compliance.
Contact us to design a manganese ore processing plant and get mining equipment latest price based on your mineral situation and requirements.
Contact Us Now
Ask us about mineral processing configuration and equipment quote! (No job, No investment)
Notice:
- We only provide mineral processing equipment and solutions; not buy and sell minerals/ ores/ materials.
- We do not recruit, don’t offer jobs, and are not interested in investments or partnerships.
- We value your privacy and keep your information safe.