Mineral Processing » Solutions » Silica Sand Processing Plant
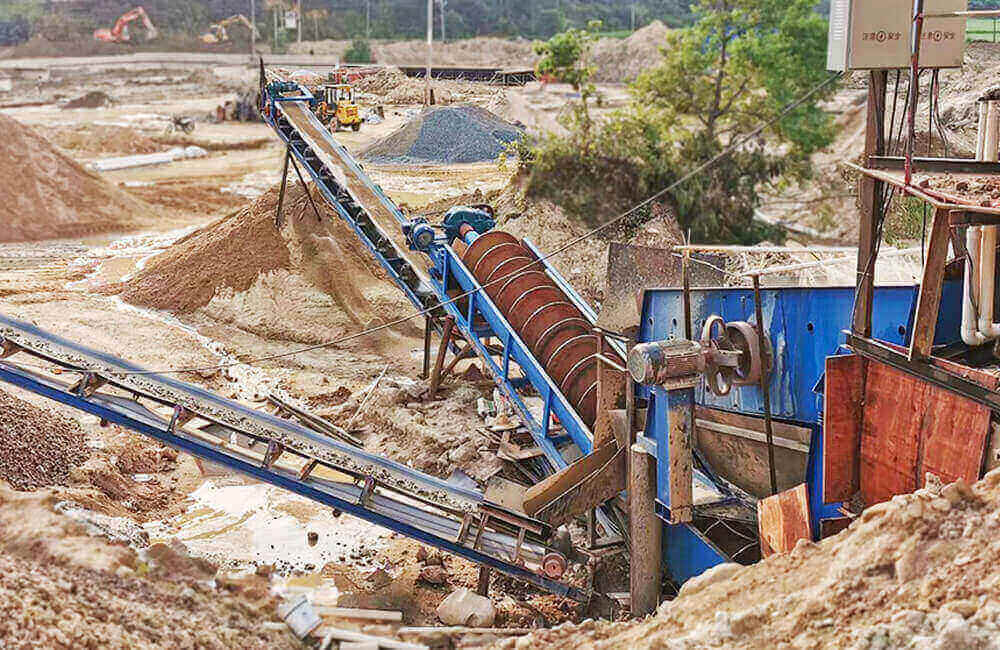
Silica Sand processing Plant
Silica sand or quartz sand, its main component is SiO2 and the content below 98.5% is called silica sand. The SiO2 content above 98.5% is called quartz sand. High-purity silica sand that meets the requirements is often obtained by mineral processing and purification.
JXSC silica sand processing plant (silica sand washing plant) helps to improve silica purity from 90% to 99.9%; mainly including washing and desliming, magnetic separation, gravity separation, flotation, and other combined processes.
silica sand beneficiation process
Silica sand beneficiation mainly includes crushing, washing, classifying, magnetic separation, flotation, etc, to remove small or trace impurities in silica sand. We supports customized silica sand washing plant solutions according to mineral composition and customer requirements.
- Silica sand crushing & grinding: The original silica sand ore is crushed and ground into finer particles for better subsequent processing.
- Silica sand washing: Remove impurities, such as soil, clay and organic matter by trommel screen, trommel scrubber or ore washer.
- Slica sand classification: The washed silica sand is classified according to the particle size, and the silica sand particles in different particle size ranges are separated, and vibrating screens or classifiers are often used.
- Silica magnetic separation: If there are magnetic impurities such as iron minerals in the silica sand, they can be removed by magnetic separation.
- Silica flotation: The flotation process can be used for silica sand ore containing flotation impurities such as diatomaceous earth.
- Concentrate treatment: During the beneficiation process, further fine treatment may be required to improve the purity and quality of the silica sand. It includes steps such as magnetic separation, gravity separation, electrical separation, etc.
- Drying: Using a rotary dryer the silica sand is treated to remove moisture for subsequent processing and application.
In practical applications, the silica sand beneficiation process is usually determined based on mineral composition and characteristics, including a combination of crushing, grinding, washing, gravity separation, magnetic or electrostatic separation and other technologies. Contact us online to obtain silica sand processing plant equipment configuration and the latest quotation!
Silica sand Processing Plant
Silica sand washing and purification plant
Raw ore information in this silica sand washing project is as follows:
- Raw sand contains 5% clay, maximum feeding size of raw sand is 20mm; contains 1% Fe2O3, need remove Fe2O3 is less than 0.02%; over 2mm size proportion in raw sand is 20%;
- Feeding capacity is 100 tons per hour;
- Finished silica sand size of customer need is less than 2mm.
This setup is a 100tph silica sand impurity removal and purification plant, that includes screening, grinding, washing, gravity & magnetic separation, dewatering. According to this raw ore information, the main equipment and flow details are as follows:
Silica Sand Washing Plant Flow
1. Feeding & screening: The excavator or loader sends the raw sand into the raw material hopper, and the sand is evenly sent to the belt conveyor by the electromagnetic vibrating feeder and then sent to the trommel screen. The trommel and its hopper have a 2 mm screen opening.
2. Grinding: The material above 2mm enters a transfer bucket through the belt conveyor, is then evenly fed to the belt conveyor by the electromagnetic vibrating feeder, and enters the ball mill to be ground to below 2mm. A sand pump delivers The ball mill output to the trommel hopper.
3. Washing: The trommel screen smaller than 2mm flows to the spiral sand washing machine by gravity. Spiral sand washing has the function of washing clay and removing muddy water. The washed sand enters a trough and is then pumped to the first stage spiral chute by the sand pump.
4. Gravity separation: The spiral chute can separate heavy minerals from sandy iron and other minerals. The spiral chute produces three outputs: concentrate, medium ore and tailings. Middling may still contain some silica sand. The concentrate from the first-stage spiral chute is sent to the concentrate chute, and the medium ore enters the second-stage spiral chute through the sand pump for reprocessing.
5. Magnetic separation: All the concentrate in the two-stage spiral chute is sent to the plate magnetic separator with sand pump to further remove Fe2O3. During this step, the iron content will drop below 0.02%.
6. Fine sand recovery system: The output of the plate magnetic separator is sent to the fine sand recovery system through the sand pump, including cyclone, dewatering screen, belt conveyor, and slurry pump. The main function is fine sand recovery and dehydration. Tailings water is recycled and enters sedimentation tanks. The dry fine sand is transported to the stockpile by the belt conveyor. This is the finished silica sand.
Key Advantages Of JXSC Silica Sand washing Plant:
- Advanced scrubbing systems for iron removal;
- AI-driven grading and quality control;
- Eco-friendly water recycling systems;
- 99.9% purity guaranteed;
- Reduce operational costs by 30% with energy-efficient methods.
Our silica sand processing plant has the advantages of high efficiency and processing capacity, low energy consumption and reasonable economy. Contact us to custom high-purity silica sand processing plant solutions and equipment 100% factory price!
Related Equipment
Contact Us Now
Ask us about mineral processing configuration and equipment quote! (No job, No investment)
Notice:
- We only provide mineral processing equipment and solutions; not buy and sell minerals/ ores/ materials.
- We do not recruit, don’t offer jobs, and are not interested in investments or partnerships.
- We value your privacy and keep your information safe.