Nickel ore is an important metal mineral resource in the national economy. With the development of the economy, people’s consumption of nickel ore resources is increasing year by year. The technology of stainless steel, the application of nickel ore rises accordingly. The number of supplies gradually increased, and people went to Indonesia and the Philippines in Southeast Asia to mine. According to the different mineral properties, nickel ore is mainly divided into copper-nickel sulfide ore and copper-nickel oxide ore. Among them, copper is the main impurity in nickel ore, followed by lead, zinc, fluorine, manganese, chromium, etc., so nickel ore beneficiation can also be said to be impurity removal. The characteristics of nickel extraction technology and beneficiation are introduced, and the characteristics of nickel ore crushing and washing process in nickel ore beneficiation design are highlighted.
1. Description of nickel ore
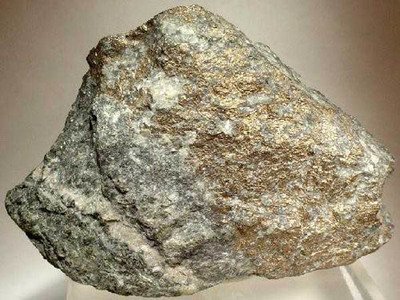
Nickel is a silver-white metal with a melting point of 1455°C, a boiling point of 2730°C, and a density of 8.90 g/cm3. It is ferromagnetic and ductile, and can conduct electricity and heat. At room temperature, nickel forms a dense oxide film on the surface in humid air, which can not only prevent further oxidation, but also resist corrosion by alkali and salt solutions.
Nickel is a non-ferrous metal mineral with strong corrosion resistance, heat resistance, good plasticity and toughness. It has a wide range of industrial uses, and is widely used in iron and steel, non-ferrous smelting, electroplating, chemical industry, machinery, military industry and other industries.
2. beneficiation of nickel
(1). Copper in copper-nickel sulfide ore mainly exists in the form of chalcopyrite, and nickel mainly exists in the form of free nickel sulfide such as fennelite and pentlandite. In addition, most of the nickel is mainly endowed in pyrrhotite in the form of similar phenomena, so the most important process of beneficiation of copper-nickel sulfide ore is flotation separation, while magnetic separation and gravity separation are usually auxiliary beneficiation methods. Collectors and foaming agents for flotation of copper sulfide minerals are often used in flotation of copper-nickel sulfide ores. A basic principle of determining the flotation process is to rather make copper enter the nickel concentrate, and avoid nickel entering the copper concentrate as much as possible. Because the nickel in the copper concentrate is lost in the smelting process, and the copper in the nickel concentrate can be recovered completely. The main beneficiation processes are priority flotation, mixed flotation, mixed-priority flotation and mixed-priority flotation + tailings recovery.
(2) Nickel laterite ore in nickel oxide ore has high iron content, low silicon and magnesium content, and 1-2% nickel content; while nickel silicate ore has low iron content, high silicon and magnesium content, and 1.6-4.0% nickel content. At present, the development and utilization of nickel oxide ore is mainly based on nickel laterite ore. Nickel oxide ore treatment usually adopts crushing, screening and other processes to remove large bedrock ore blocks with weak weathering degree and low nickel content in advance, and the enrichment ratio is relatively low. Because nickel in nickel oxide ore is often dispersed in gangue minerals in the same quality and shape, and the particle size is very fine, it is difficult to obtain good results by direct processing by mechanical beneficiation. The beneficiation methods mainly include hydrometallurgy and pyrometallurgy.
The extraction of nickel process generally consists of crushing, sieving, washing, gravity separation, grinding, and slurry concentration, or the nickel leaching method. The target element nickel distribution varies with the nature of the ore, mostly contained in fine-grained grades. For example, the nickel minerals of the Ramu laterite mine in Papua New Guinea are mainly enriched in fine mud of -53 μm. There are uncommon, such as Cameroon cobalt nickel manganese laterite ore, the nickel are mainly concentrated in +0. In the grain size above 3mm, the Philippine BNML nickel ore limonite + ore nickel grade above 50mm 2. 89%, the coarser the grade of ore, the higher the grade of nickel.
3. nickel ore Beneficiation Equipment
1. Crushing equipment
A columnar rock often accompanies nickel ore with incomplete weathering. The block size may exceed 1m. If you don’t crush them, only use the original ore bin to control the ore size. The rock is easily stuck in the sieve hole, affects the normal supply during the nickel extraction process. Therefore, it is recommended that the laterite mine should be crushed better before washing.
Mainly stone crushers such as jaw crusher, impact crusher, hammer crusher, cone crusher and roller crushers, all have a common disadvantage that they cannot effectively handle materials with high mud content, high water content and high viscosity. The double roller crusher can effectively overcome the shortcomings of conventional crusher. the working principle of double roller crusher is that the shearing force acts directly on the ore material through the high-torque, low-speed transmission system, so that the force is along the weak and fragile parts of the material. Produces a huge crushing force to break it, forming a unique crushing particle size control technology. When the crusher is working, the material can be discharged into the upper part of the whole machine. The size of the feed port is larger than that of any crusher, and it is not easy to cause the blockage. The discharge port is also very large, and almost the entire lower part of the equipment can be discharged. product. The movement of the double-toothed tooth causes the material to be broken and can be forcibly discharged, so it is especially suitable for viscous materials and materials with high water content, and the discharge opening is not blocked.
2. washing equipment
The washing equipment used in the nickel mining process mainly includes trommel scrubber, spiral washing machine and stirring scrubbing tank. The laterite nickel mine washing system is composed of a cylindrical gold trommel washing machine and two spiral washing machines. The Australian laterite nickel ore is washed by a trommel scrubber. The specifications of the trommel scrubber are: 5m × 11. 9m for limonite, 4m × 7. 4m is used for residual ore. The grit of the first-stage hydrocyclone of laterite mine is fed into the mixing scrubbing tank and then graded into the second-stage hydrocyclone. The Papua New Guinea laterite nickel mine adopts a combined washing method of a cylinder washing machine and a spiral washer machine. The gold trommel washing machine has a specification of 3m × 10m, and the tank type washing machine has a specification of LW36′′ × 35′. Generally speaking, after a section of crushing, the cylinder size of the cylinder is used to feed the ore – 300mm; the size of the log washing machine is – 50mm. For most of the laterite nickel ore, the nickel-cobalt is mainly rich in – In the 3mm grain class, the grain size above +3mm is discarded as waste rock. For example, 3mm ~ 50mm of laterite mine is recycled by sanding of the log washing machine, and the material of +50mm is thrown through the cylinder of the cylinder washing machine. Waste.
3. Separation equipment
The particle size of the sulfide mineral aggregates in nickel ore is not uniform, and the nickel sulfide ore is prone to over-crushing and oxidation. And it contains a large amount of magnesium-containing gangue minerals that are easy to muddy and have good buoyancy. The beneficiation methods for this type of ore include gravity separation, flotation, leaching and combined separation. The equipment used includes dense medium cyclone, flotation machine.
4. Dewatering equipment
The water content of the material after flotation is relatively large. To speed up the drying speed of the product, it is usually dehydrated and separated by a thickener, and then dried by a dryer to obtain the finished product. The tailings are dehydrated through the tailings dry discharge process, and the tailings are moved to the tailings storage. The dewatering equipment used includes dewatering machine, filter press, thickener.
Beneficiation of nickel research has a very positive effect on the nickel mining process, extraction of manganese, extraction tin and other mining minerals. Nickel ore processing is constantly upgrading. JXSC provides full of nickel ore processing equipment for nickel mining companies around the world. Contact us to get the mining equipment price including stone crusher, grinding equipment, ore washing machine, flotation machine, dewatering machine.