10TPH Feldspar Processing Plant In Nigeria
We guarantee the high quality machine in the mineral processing industry, established in 40+ years of experience!
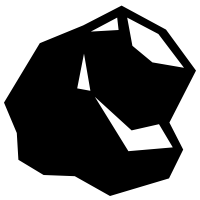
minerals
Raw feldspar ore contains iron, calcium, mica and other impurities
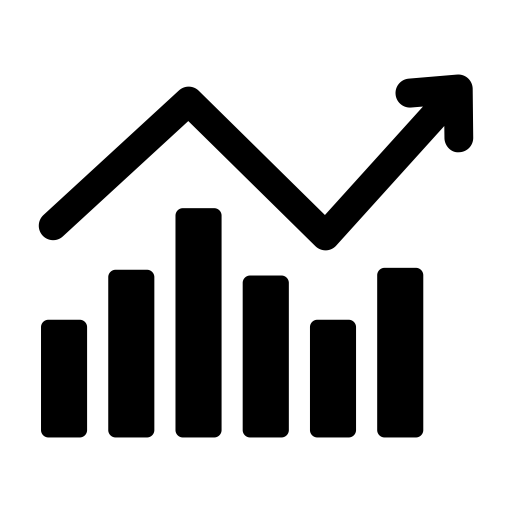
capacity
10TPH
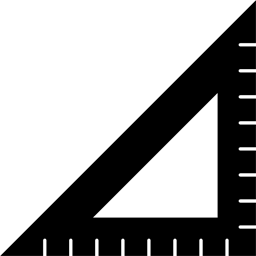
feed size
0-200mm
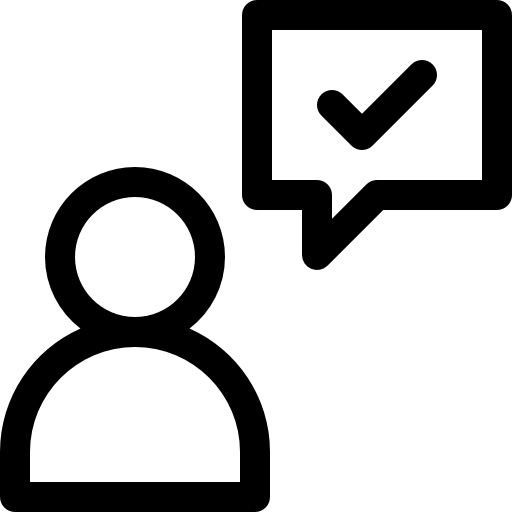
Customer's request
remove iron, mica and other impurities to obtain high grade feldspar
process flow
10TPH Feldspar Processing Plant
1. Crushing & Screening: jaw crusher, vibrating screen
Utilize rough jaw crusher, fine jaw crusher and vibrating screen to form a closed crushing circuit, so as to make 200mm rock ore down to 20mm. Thus, it makes sure the particle size of the material entering the grinding section is qualified.
2. Grinding section: ball mill, spiral classifier
Utilize ball mill and spiral classifier to form closed grinding circuit, so as to achieve more than 90% discharging size 200mesh(0.074mm). Thus, it makes sure the particle size of the material entering the flotation section is qualified.
3. Magnetic separation: magnetic separator
A two-stage magnetic separation process of low-intensity magnetic separation and high-intensity magnetic separation was used to remove magnetic minerals in feldspar ore to the maximum extent. Low-intensity magnetic separation can remove magnetite(Fe3O4), and high-intensity magnetic separation can remove hematite, limonite, ilmenite(Fe2O3).
4. Flotation section: flotation machine
The flotation process is used to remove impurities in the feldspar ore further, so as to obtain high grade feldspar concentrate.
5. Dewatering process for concentrate: thickener, disc vacuum filter machine
The dewatering process for the concentrate utilizes a thickener and a disc vacuum filter machine. Use a slurry pump to send concentrate to the thickener, the overflow of the thickener goes to a clear water pond, and the underflow goes to the disc filter machine for dehydration. After being dehydrated by a disc filter machine, the moisture concentration is less than 10%.
6. Tailing dry discharging process: cone thickener, plate filter machine
All tailings are first pumped to the cone thickener to adjust the suitable concentration. The overflow of the cone thickener goes to the recycled clear water pond, and the underflow goes to the plate filter machine for dehydration. Finally, the moisture of the tailing is less than 10%, which is the tailing dry discharging process.
Contact Us Now
Ask us about mineral processing configuration and equipment quote! (No job, No investment)
Notice:
- We only provide mineral processing equipment and solutions; not buy and sell minerals/ ores/ materials.
- We do not recruit, don’t offer jobs, and are not interested in investments or partnerships.
- We value your privacy and keep your information safe.