Mineral Processing » Solutions » Cobalt Ore Processing
Cobalt Ore Processing
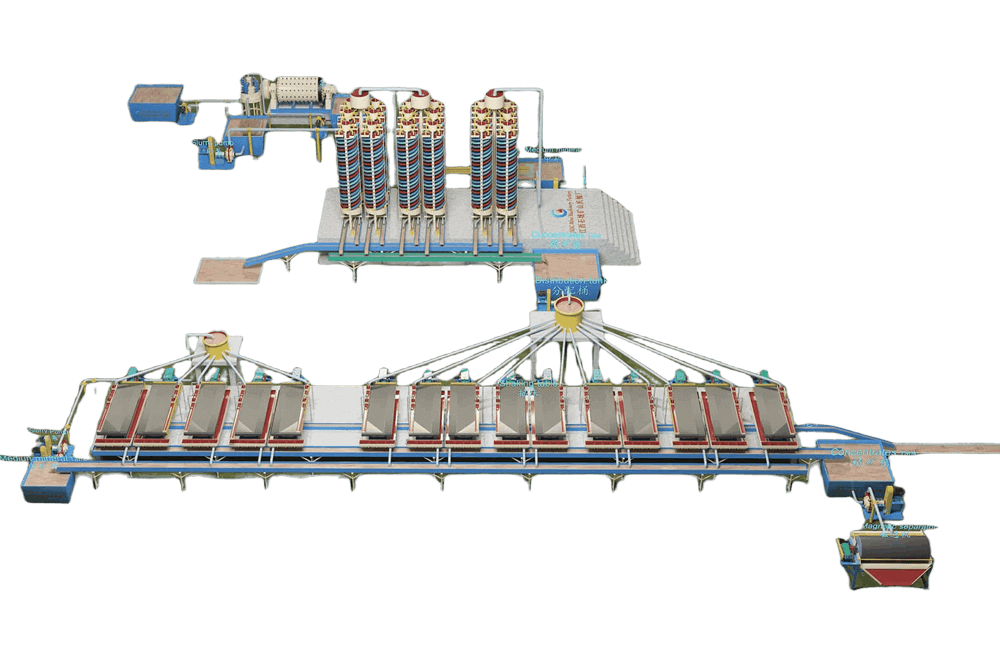
Cobalt ore is mostly associated with copper-cobalt ore, nickel-cobalt ore, iron-bearing cobalt ore, and manganese-cobalt ore. It may contain impurities or other harmful substances such as sulfur, arsenic, etc.
JXSC supports custom cobalt beneficiation plants; these impurities can be removed to improve the quality and purity of cobalt. It mainly includes crushing, grinding, flotation, gravity separation, magnetic separation, leaching, etc.
Cobalt Beneficiation process
Cobalt ore beneficiation is extracting and separating valuable cobalt minerals from ore.
- Magnetic separation method: Since cobalt minerals usually have strong magnetism, cobalt minerals are separated from non-magnetic minerals by magnetic separation. It is especially suitable for sorting ores containing magnetic minerals like iron-cobalt.
- Flotation method: suitable for sorting cobalt ore containing sulfide minerals, such as copper-cobalt ore and nickel-cobalt ore. Cobalt minerals can be separated from other ores by adding specific flotation agents in the flotation cell.
- Gravity separation method: According to the difference in density between cobalt minerals and other ores, they can be stratified by gravity separation and then separated by process steps such as concentration and filtration. It is suitable for sorting cobalt ore containing barite and light impurities.
- Acid leaching or leaching: It can be used to separate some low-grade cobalt ores. Cobalt minerals are dissolved or leached and separated from other ores by placing the ores in an acidic or alkaline solution.
Cobalt beneficiation process may also involve steps such as grinding, screening, washing and drying to improve the quality and separation of ore further. The specific beneficiation process and optimization must be researched and tested according to the ore situation.
Cobalt Ore processing Plant
1. Crushing and grinding: it is crushed into an appropriate particle size through the crushing process. Crushing equipment such as jaw crushers and cone crushers are often used. The crushed ore usually enters the ball mill for further fine grinding to make the ore particle size finer.
2. Flotation: The ore after grinding usually contains cobalt minerals and various metal minerals. Flotation is one of the commonly used ore separation techniques. The target minerals are floated with the foam by suspending the ore in an aqueous solution containing a specific agent. It usually includes the stages of rough separation, selection and sweeping.
3. Concentrate treatment: The cobalt ore concentrate obtained after flotation needs further treatment. It may include further magnetic separation, gravity separation (spiral chute, shaking table), or other combined processes to remove residual impurities and improve the grade and purity of the cobalt mineral.
4. Concentration and drying: To further increase the cobalt ore content, the flotation slurry needs to be concentrated. Typically, filter press is used to separate the liquid from the solids to increase the cobalt ore content.
Cobalt ore processing plants usually include the above four steps. The specific process will be customized according to the details of the mineral. Contact us for more details and equipment prices!
Contact Us Now
Ask us about mineral processing configuration and equipment quote! (No job, No investment)
Notice:
- We only provide mineral processing equipment and solutions; not buy and sell minerals/ ores/ materials.
- We do not recruit, don’t offer jobs, and are not interested in investments or partnerships.
- We value your privacy and keep your information safe.