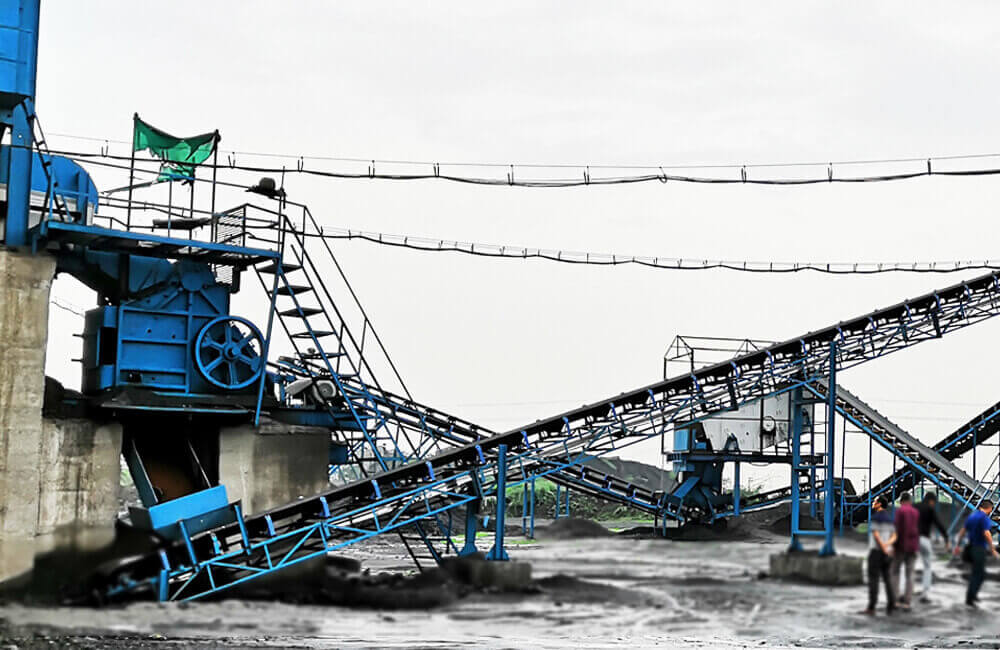
Graphite Ore Processing
Graphite ore beneficiation includes gravity separation, flotation, and magnetic and electric separation; it is widely used in separating natural graphite, flake graphite, crystalline graphite, graphite in granite, etc.
According to the specific composition and properties of the ore, JXSC will combine multiple methods for comprehensive processing to achieve the best separation effect.
Graphite beneficiation process
Graphite ore beneficiation refers to separating valuable minerals from raw graphite ore to obtain products with higher purity and more suitable for specific purposes. Usually, multiple beneficiation methods are usually combined to achieve higher grade and purity graphite products.
1. Hand selection: The raw ore grade of aphanitic graphite is generally high, and the carbon content is 60-80%. The product can be obtained after hand selection, crushing and grinding.
2. Gravity Separation: The symbiotic minerals of graphite ore mainly include pyrite, pyrrhotite, limonite, etc., followed by zircon, white titanium, monazite, scheelite, diopside, and occasionally apatite and other minerals. Heavy minerals are separated by gravity separation, which is often combined with flotation to obtain rough concentrate mainly composed of graphite.
3. Flotation Separation: The grade of flotation graphite concentrate can usually reach 80% to 90%, and the purity can reach about 98% using multi-stage grinding and separation. It can effectively protect graphite flakes and improve the grade of graphite.
3. Magnetic separation: It is suitable for separating magnetic minerals in graphite ore.
4. Electric separation: Graphite ore has good conductivity, while gangue minerals (such as feldspar, quartz, pyrite, etc.) have poor conductivity. Based on this difference, it can be separated by electro-separation.
Graphite processing plant
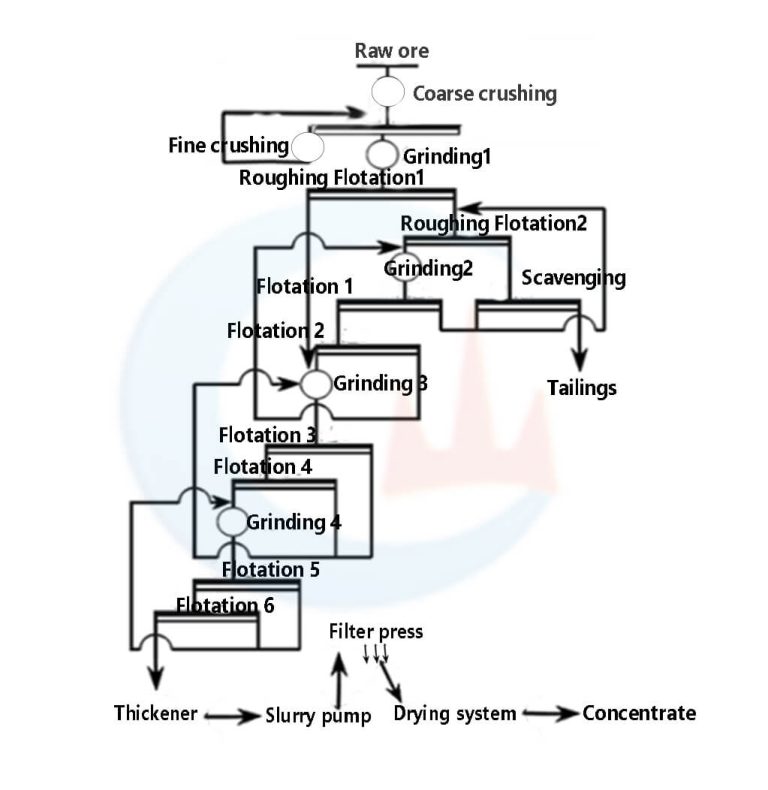
Graphite Flotation process plant
The general graphite ore process includes crushing – screening – grinding – flotation – dehydration – drying.
1. Preparatory process (crushing, screening and grinding)
Since the hardness of graphite ore is generally medium-hard or soft, and the grade is generally between 2% and 10%, it usually adopts three-stage open circuit, two-stage open circuit or one-stage crushing process. Ensure that the graphite flakes are not damaged and the quality of the concentrate meets the requirements.
2. Flotation process (rough sorting, sweeping and concentrate separation)
Due to the high value of graphite, the three-stage flotation machines process can realize more efficient extraction of graphite particles from raw ore, gradually improve the grade and purity of graphite concentrate and simultaneously increase capacity and economic benefits.
3. Concentrate treatment (dehydration, drying, screening, packaging)
Dewatering screens, filter presses or rotary dryers are commonly used to dehydrate graphite ore concentrates.
Related Equipment
Contact Us Now
Ask us about mineral processing configuration and equipment quote! (No job, No investment)
Notice:
- We only provide mineral processing equipment and solutions; not buy and sell minerals/ ores/ materials.
- We do not recruit, don’t offer jobs, and are not interested in investments or partnerships.
- We value your privacy and keep your information safe.