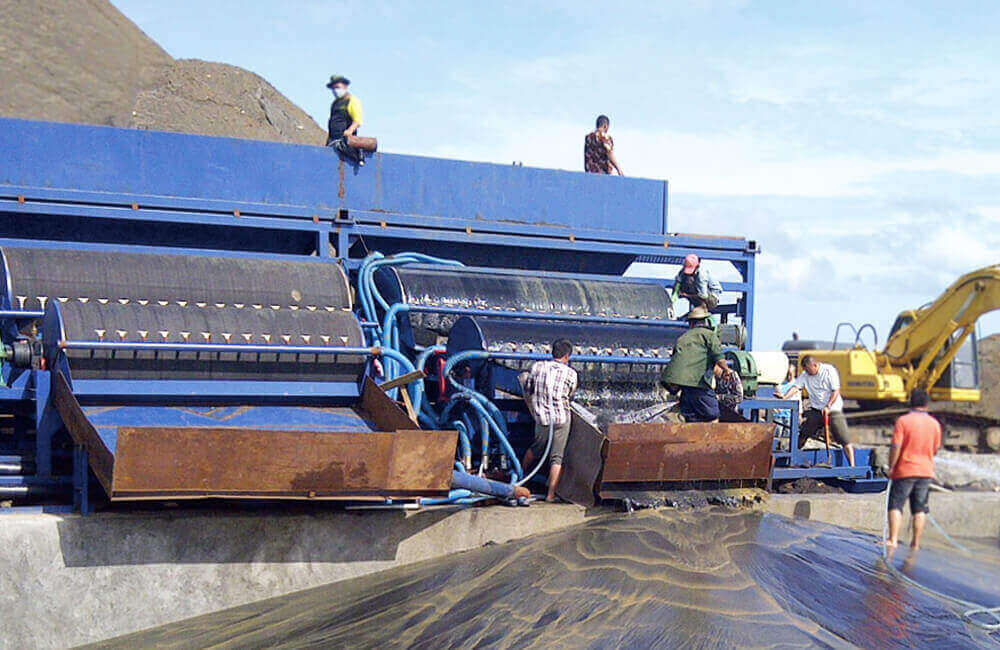
Hematite Separation Process
Hematite is iron oxide, a weakly magnetic iron mineral with an iron content of up to 70%. Mineral separation is the process of converting raw ore into high-quality products while meeting the market demand for steel production.
Hematite separation processes usually include crushing, grinding, gravity separation, flotation and strong magnetic separation or combined processes.
Hematite beneficiation process
The hematite separation process mainly involves various methods to extract valuable minerals from the ore, including crushing, grinding, magnetic separation and flotation. It is suitable for processing hematite with complex structure such as hematite and impurities with uneven particle size distribution, ores with more fine particles, ores with less magnetite, and gangue minerals containing quartz or kaolin.
- Crushing & Grinding: Crushing limonite ore into smaller particles to increase the surface area for chemical reactions. It is then ground into powder to further reduce the size to facilitate mineral separation.
- Magnetic separation: Taking advantage of the differences in magnetic properties between different minerals, iron can be effectively extracted. High-intensity magnetic separators are often used to remove impurities and improve the quality of hematite concentrates.
- Flotation: It is another key step in the mineral processing process, which separates the desired minerals from the gangue material through the use of specific chemical reagents based on the hydrophobicity of the gangue material.
Hematite Separation plant
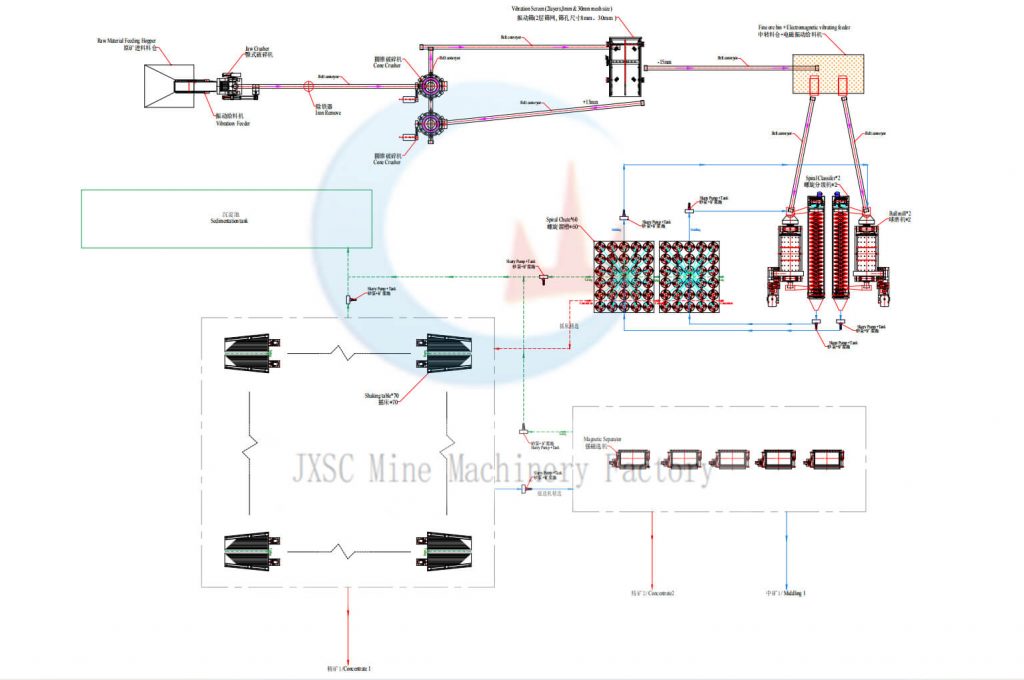
100TPH hematite separation process plant
This is a complete 100tph hematite processing plant. The main equipment includes vibrating feeder, jaw crusher, cone crusher, vibrating screen, ball mill, spiral classifier, spiral chute, vibrating table, magnetic separator, etc.
1. Feeding and crushing system:
Using a vibrating feeder to feed raw materials (below 500mm) stably and evenly into the primary jaw crusher. The primary jaw crusher is used to primary crush large rocks below about 150mm, and then the output of the primary jaw crusher will enter the first cone crusher for secondary crushing.
The output of the first cone crusher is about 40mm or less, which enters two sets of vibrating screens (15mm and 40mm two-layer screens, the 40mm screen plays a protective role), and 0-15mm fine materials are screened out and stored on the ground. It enters the second fine cone crusher and is crushed again. The output of the second fine cone crusher will also be sent to the vibrating screen, and the 0-15mm screened out material will be sent to the fine ore bin by the belt conveyor.
2. Grinding system: Powdered materials of 0-15mm enter the fine ore bin in front of the ball mill. A small vibrating feeder is installed below the transfer bin; powdery materials are smoothly transported to the ball mill through a belt conveyor. The function of the ball mill and spiral classifier is to grind the materials into fine powder to release as much Fe3O4 as possible from the hematite ore to obtain a 100-mesh to 200-mesh slurry.
3. Gravity separation system: The slurry is first sent into the tank, and then pumped into the spiral chute to concentrate the hematite. The hematite focus in the spiral chute is then pumped into shaking tables to be refined again.
4. Magnetic separation system: The hematite concentrate from the gravity separation system will be sent to the magnetic separator for re-refining to ensure a higher grade of hematite
5. Tailings system: Tailings from the gravity separator system and magnetic separator system will be pumped into settling tanks.
Contact us to customize the hematite processing process and get the latest quotation of equipment.
Related Equipment
Contact Us Now
Ask us about mineral processing configuration and equipment quote! (No job, No investment)
Notice:
- We only provide mineral processing equipment and solutions; not buy and sell minerals/ ores/ materials.
- We do not recruit, don’t offer jobs, and are not interested in investments or partnerships.
- We value your privacy and keep your information safe.