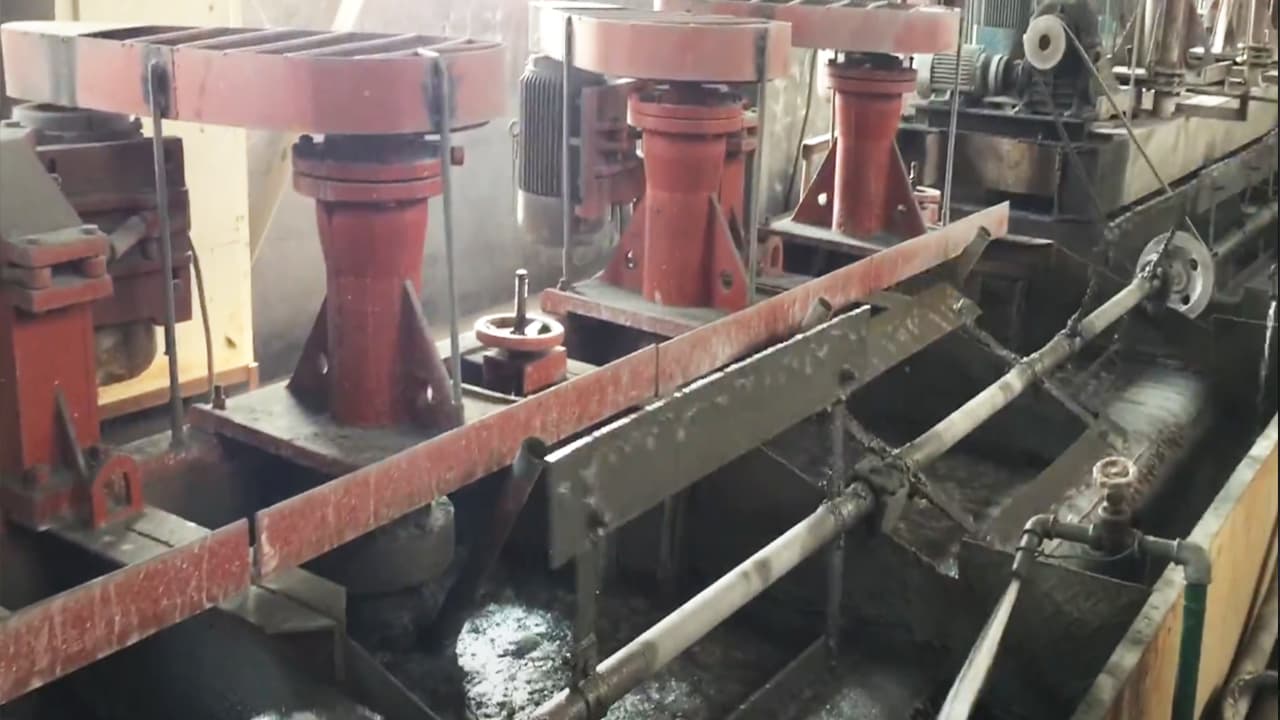
Sulfide Ore Processing
This sulfide rock ore processing plant suitable for separating sulfide rock gold, copper, silver, zinc, lead, fluorite ore, etc.
Usually can reach about 85-90% depending on material conditions. We support custom sulfide ore processing plant and equipment to max your mineral recovery rate.
Sulfide ore beneficiation process
Sulfide ore beneficiation process is the physical or chemical treatment of sulfide ores, from which valuable sulfide minerals and waste rocks are separated. Non-valuable minerals are removed as much as possible to obtain a high-grade concentrate. In general, the main process of sulfide ore beneficiation is as follows:
- Flotation Separation
Flotation is a widely used method for separating and enriching valuable minerals from gangue minerals in sulfide ores. Primarily water and specific chemicals are used to separate sulfide minerals from impurities. Especially suitable for sulfide metal minerals, such as pyrite, chalcopyrite, sphalerite, etc.
- Gravity Separation
Gravity separation is suitable for situations where the specific gravity of certain sulfide ores is significantly greater than that of waste rocks. Separation and extraction can be achieved by using density suspension or dense medium suspension to settle the sulfide minerals with larger specific gravity and float the lighter waste rocks.
- Magnetic Separation
Mainly used for ores containing magnetic sulfide minerals. Applying a magnetic field separates the magnetic sulfide minerals from the non-magnetic waste rocks, thereby obtaining sulfide minerals with higher purity.
The beneficiation process for a sulfide ore may involve a combination process to ensure efficient, economical and environmentally friendly extraction and processing. We will also consider resource utilization and environmental protection requirements during the beneficiation process to minimize environmental impact.
Sulfide Ore Processing Plant
Sulfide ore flotation process plant
The complete sulfide ore flotation plant main equipment and flow details as follows:
- Jaw crusher
- Vibration screen
- Ball mill
- Spiral classifier
- Flotation machine
- Thickener
- Disc vacuum filter
1. Crushing System
The chute feeder feeds raw materials into the primary jaw crusher evenly and can feed materials of 0-300mm. A grid vibrating feeder can be used with larger size and capacity. The primary jaw crusher then crushes the large rocks to approximately 0-80mm particle size. Then the output material is transported to the fine jaw crusher and crushed again to less than 25mm. The output of the fine jaw crusher is transported to the vibrating screen to screen out 0-25mm, and more than 25mm materials will continue to be crushed to the required particle size and finally enter the grinding system. The smaller the feed particle size of the ball mill, the better, and the grinding efficiency will be much higher. Therefore, a three-stage crusher can be equipped in the crushing system to make the feed particle size of the ball mill smaller (0-5mm, 0-8mm or 0-10mm).
2. Grinding System
Before the 0-25mm material is fed into the ball mill, there is enough 0-25mm material in the storage bin, and the crushing system can work separately from the grinding system. Then the 0-25mm material is fed into the ball mill through the belt conveyor by the swing or electromagnetic vibrating feeder. Since the flotation process requires 200-mesh materials, it is necessary to cooperate with a ball mill and a spiral classifier. The 200-mesh slurry is reached from the overflow of the classifier, and the coarse particles in the underflow will return to the ball mill for grinding again to obtain the closed-circuit grinding effect.
3. Flotation System
The 200-mesh slurry is first pumped to the mixing tank through the slurry pump to ensure that the materials are fully mixed. Then it enters the flotation machine from the stirring tank, and different chemicals need to be added to the flotation machine to separate different minerals. The flotation process includes primary, secondary, and final selection to increase the grade of the processed minerals to the highest level. If a higher grade is required, more rinses are needed. After passing through the flotation system, the concentrate will be obtained.
4. Concentrate Filtration System
After passing through the flotation system, high-grade minerals such as copper, zinc, lead, and fluorite are concentrated by a thickener to make them denser. It is then sent to a disc vacuum filter to filter the water and get more dry concentrate minerals. Then it can be dried in the sun or dried in a dryer to obtain completely dry minerals to achieve the purpose of concentrate.
This Sulfide ore flotation processing plant is highly effective in recovering sulfide minerals. At the same time, it suitable for flotation of sulfide silver, lead-zinc, fluorite ore, copper and gold. The beneficiation plant efficiency and the recovery rate are high, especially effective for fine-grained ores, high-quality concentrates can be obtained, and mineral resources can be fully utilized. The sulfide flotation flow design and capacity can be customized as per rock minerals conditions.
Related Equipment
Contact Us Now
Ask us about mineral processing configuration and equipment quote! (No job, No investment)
Notice:
- We only provide mineral processing equipment and solutions; not buy and sell minerals/ ores/ materials.
- We do not recruit, don’t offer jobs, and are not interested in investments or partnerships.
- We value your privacy and keep your information safe.